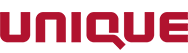
PET bottle preform injection molding plant integrated planning for water, electricity, and gas: the golden key to improving production efficiency!
In recent years, the sustainable operation of the injection molding industry has been increasingly valued. In achieving a green production process for PET bottle preform injection molding systems, the rational planning of water, electricity, and gas is crucial. This article will explore the key points of integrated planning for water, electricity, and gas in injection molding machine production lines and provide feasible implementation plans for production enterprises.
1. Water supply system planning
In the planning of the water supply system in an injection molding plant, the primary task is to ensure the stable supply and recycling of water resources. Closed cooling towers and open cooling towers are two common cooling systems, and choosing the appropriate system is crucial.
1) Closed cooling towers achieve the isolation of water and air by using a coolant in the pipelines. This can reduce impurities in the water, reduce the risk of pipeline rusting, and improve the stability of circulating water. However, comparatively, closed cooling towers have higher investment and operating costs.
2) Open cooling towers expose water to the air for cooling. This system is relatively simple and has lower costs. However, it is susceptible to external pollution and climate changes, requiring more frequent maintenance.
2. Power supply system planning
The planning of the power supply system directly affects the normal operation and energy efficiency of the factory equipment. Key points include:
1) Power load assessment: A detailed evaluation of the power demand in the injection molding workshop should be conducted to ensure that the power supply system can meet peak loads and avoid production losses due to inadequate power supply.
2) Selection of energy-efficient equipment: Choose high-efficiency, low-energy-consumption equipment, such as frequency converters and LED lighting, to reduce energy costs.
3. Gas supply system planning
The planning of the gas supply system in an injection molding plant needs to consider the gas requirements during the production process, as well as the requirements for gas purity and stability. The choice of gas type can be based on the needs of the production process.
4. Intelligent monitoring system
Introducing an intelligent monitoring system for real-time monitoring and control of the integrated water, electricity, and gas supply is an effective means to improve production efficiency and reduce costs. Key points include:
Sensor monitoring: Install sensors at critical points to monitor the usage of water, electricity, and gas in real-time, enabling timely detection of problems and appropriate measures.
Remote control: Establish a remote monitoring and control system, allowing management personnel to supervise and adjust the water, electricity, and gas systems anytime and anywhere, thereby improving response speed.
5. Risk assessment and safety planning
When planning the integrated water, electricity, and gas supply system for an injection molding plant, potential risks must be fully considered, and corresponding safety plans should be formulated. Key points include:
1) Risk assessment of disasters: Evaluate geological and meteorological disasters, and take appropriate safety measures to ensure the safe operation of factory facilities.
2) Emergency plans: Develop emergency plans for the water, electricity, and gas supply system, predict and respond to potential problems, minimizing losses.
In summary, by comprehensively considering the planning of water supply, power supply, and gas supply, as well as incorporating elements of intelligent monitoring and risk safety management, the integrated water, electricity, and gas supply system in an injection molding workshop can better adapt to the future industrial development needs. This not only helps improve production efficiency and reduce energy costs but also aligns with the principles of green environmental protection, laying a solid foundation for the sustainable operation of the plant. By choosing suitable water, electricity, and gas supply systems, combined with green energy and intelligent monitoring, an injection molding plant can create an efficient and sustainable production environment, making positive contributions to the industry's development.